The Brief
The project brief was to design and manufacture a resonator guitar fit for a consumer. This involved creating prototypes, SolidWorks designs, sourcing materials and the manufacture of the resonator guitar. We had a total budget of €200 to purchase any raw materials or pre-manufactured components needed. The final report required a bill of bulk materials, design drawings, assembly instructions and details of the manufacturing process.
Before the invention of modern amplifiers resonator guitars were used to increase the volume compared to a standard acoustic guitar. In the 20s and 30s acoustic guitars were being overwhelmed in brass bands. In a resonator guitar the energy in the string propagates and transfers to the spun cones under the faceplate causing the sound to resonate.
Design
The first stage of the project was to research resonator guitars including visiting a number of guitar stores and researching the history of resonator guitars. We then progressed to creating prototypes and advancing through models. This involved a 3D printed model, a 2.5D and 3D cardboard model. These prototypes allowed us to define the size, style and shape of our guitar.
We first created a 2.5D prototype to assist us in visualizing the spatial relations in different basic elements such as the neck length and the body. Both our 2.5D and 3D prototypes were simple models made from cardboard, tape and string. These simple representations of our designs allowed us to consider proportions, dimensions and ergonomics of our components. Building the 3D prototype also enabled us to review the assembly process for our guitar such as the order and any potential issues. This stage led us to focus on the attachment of the neck to the metal body of the guitar as this step would be the most awkward in the assembly process.
The final prototype we made was the 3D Printed scale model which depicted the spatial relations of our guitar design on a smaller scale. We used an Ultimaker 2 to print the components and finished it with spray paints suitable for use with plastic.
Following the completion of our design concept, we then decided which components we wanted to manufacture or purchase. The headstock, neck and body would be manufactured while smaller components including the tailpiece, strings and machine heads would be purchased. We also decided to purchase the cone and bridge as we were only making one guitar.
All of our designs of each individual component of the guitar were created and finalised in SolidWorks. The neck and headstock of our guitar were manufactured from maple using a CNC machine. The metal body of the guitar was cut from mild steel 1mm thick. We opted for steel as we preferred the qualities it would give the sound and appearance. The neck and headstock were treated with a clear varnish and the metal body of the guitar was primed and sprayed black before the assembly process.
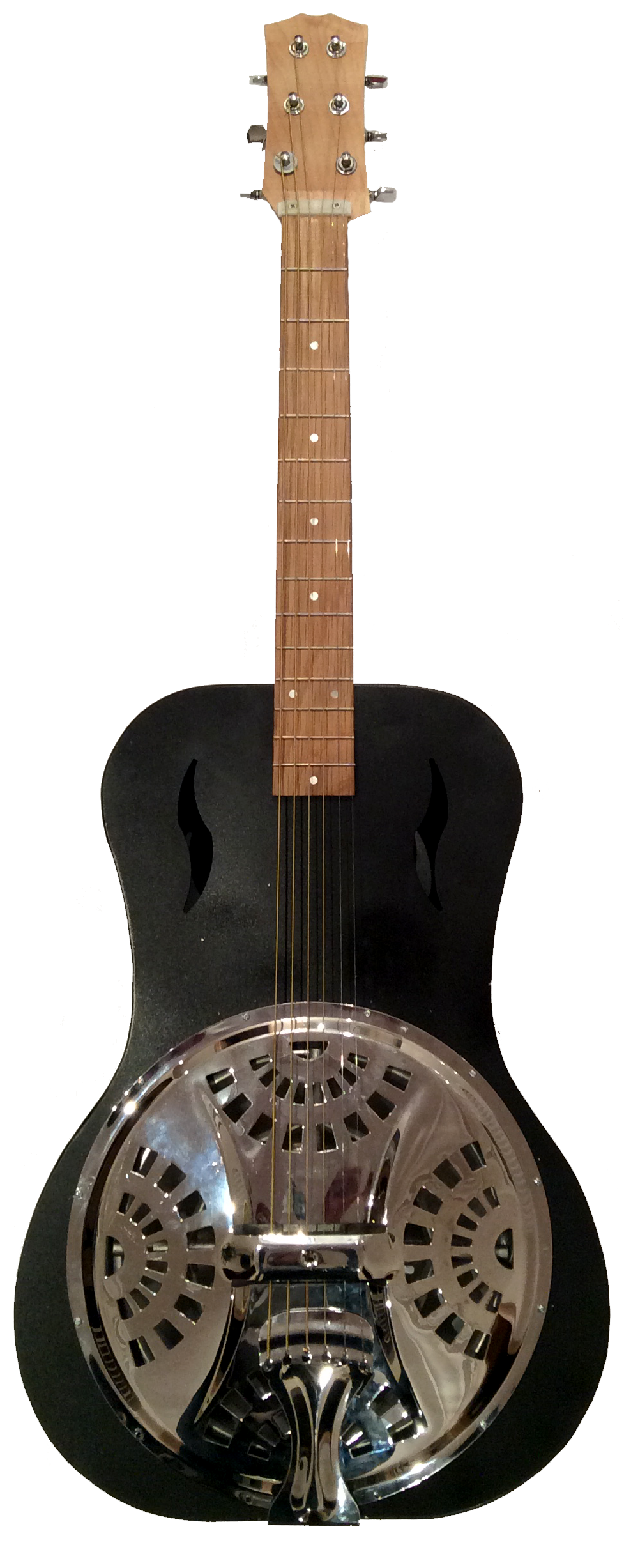
Our Groups finished Resonator Guitar
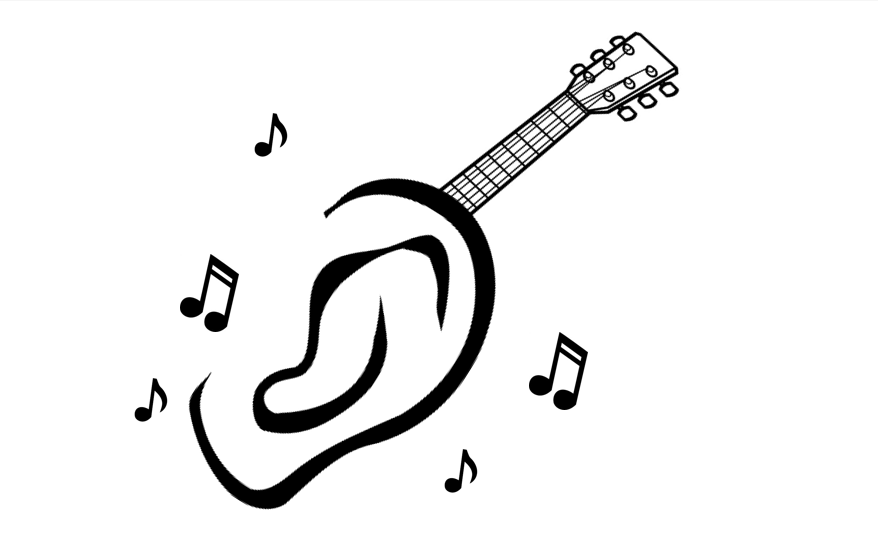
Mock Logo for Basilar Guitars
Finance & Marketing
A sub task to this design project was a Dragons Den style competition. We had to create a business plan for our guitar company and present to a panel of judges. This included logistics, finance, production, manufacturing and marketing plans.
Our guitar company name was ‘Basilar Guitars’. It was inspired by the basilar membrane in the ear, which resonates translating sound waves. We felt the unique name highlighted the core of the business - resonance.
Conclusion
Upon completion of the guitar project these were my thoughts:
“This project was a lot more challenging than I first anticipated but it is hugely rewarding to see all the work come together in the finished guitar. While I learnt a lot about the manufacturing process over the course of this project, I learnt just as much about project management and teamwork work. I really enjoyed the prototyping and design stages. The prototypes helped us form a definite idea of the design features and qualities we wanted to prioritise in our own guitar. Though many hours were spent editing and changing designs, ringing suppliers, and assembling our guitar, I’ve found the experience hugely interesting and I’ve learnt that there are a lot of steps and variables to even the simplest of issues.”
Emily Colwell 5th April 2016
This project allowed us to develop a number of skills including problem solving, communication, experimentation, quantitative analysis, and project costing among others. Key to the success of this project was outlining and sticking to our project timeline early in the project. Beginning tasks early, such as design stages like SolidWorks drawings are time consuming and starting early allows for any alterations to design decisions.
Designing the resonator guitar from start to finish gave us invaluable experience and it was highly rewarding seeing our concept develop from designs, to a 2.5D cardboard model guitar, and finally to the finished metal-body resonator guitar.
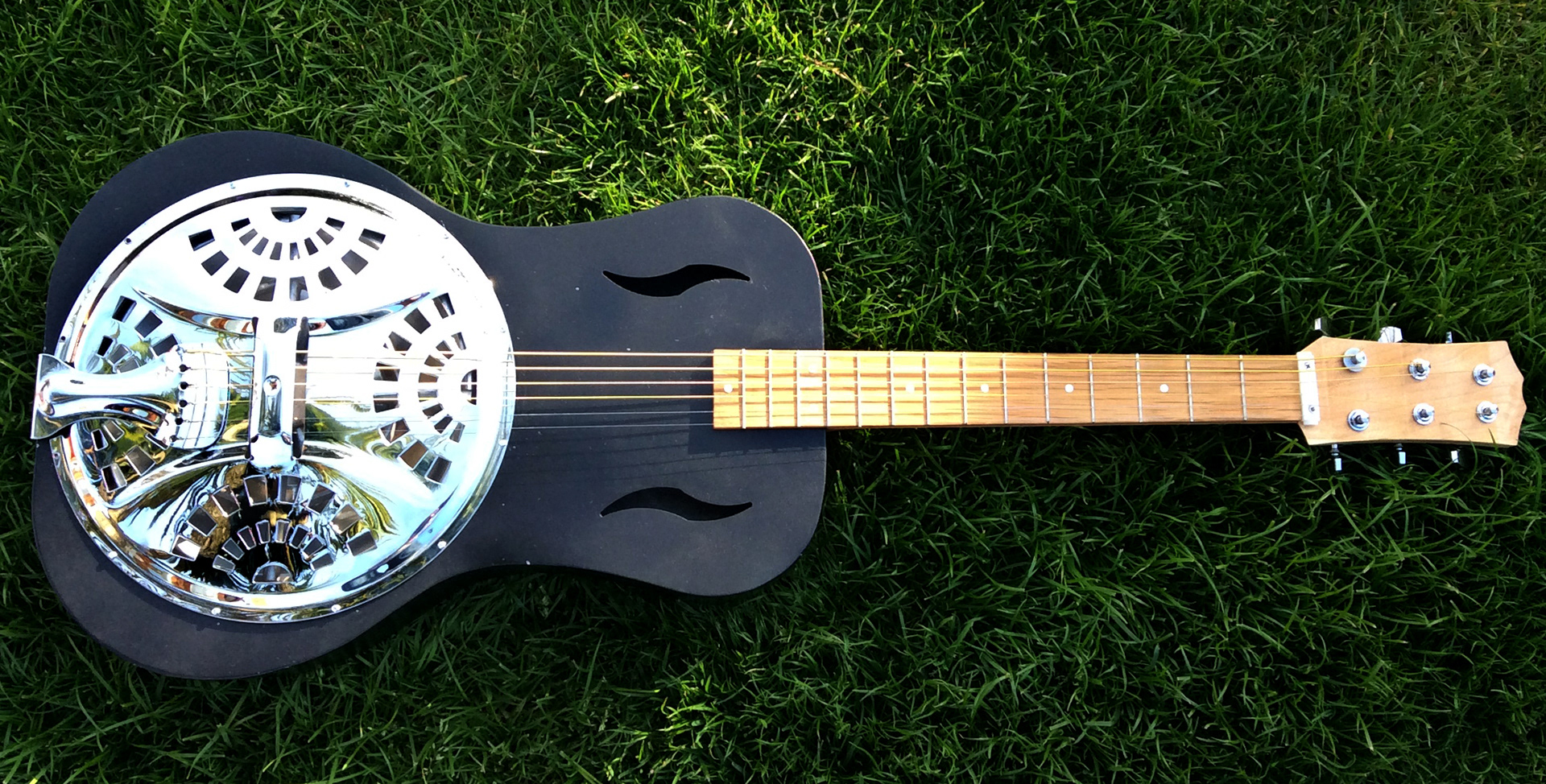
The Finished Resonator Guitar
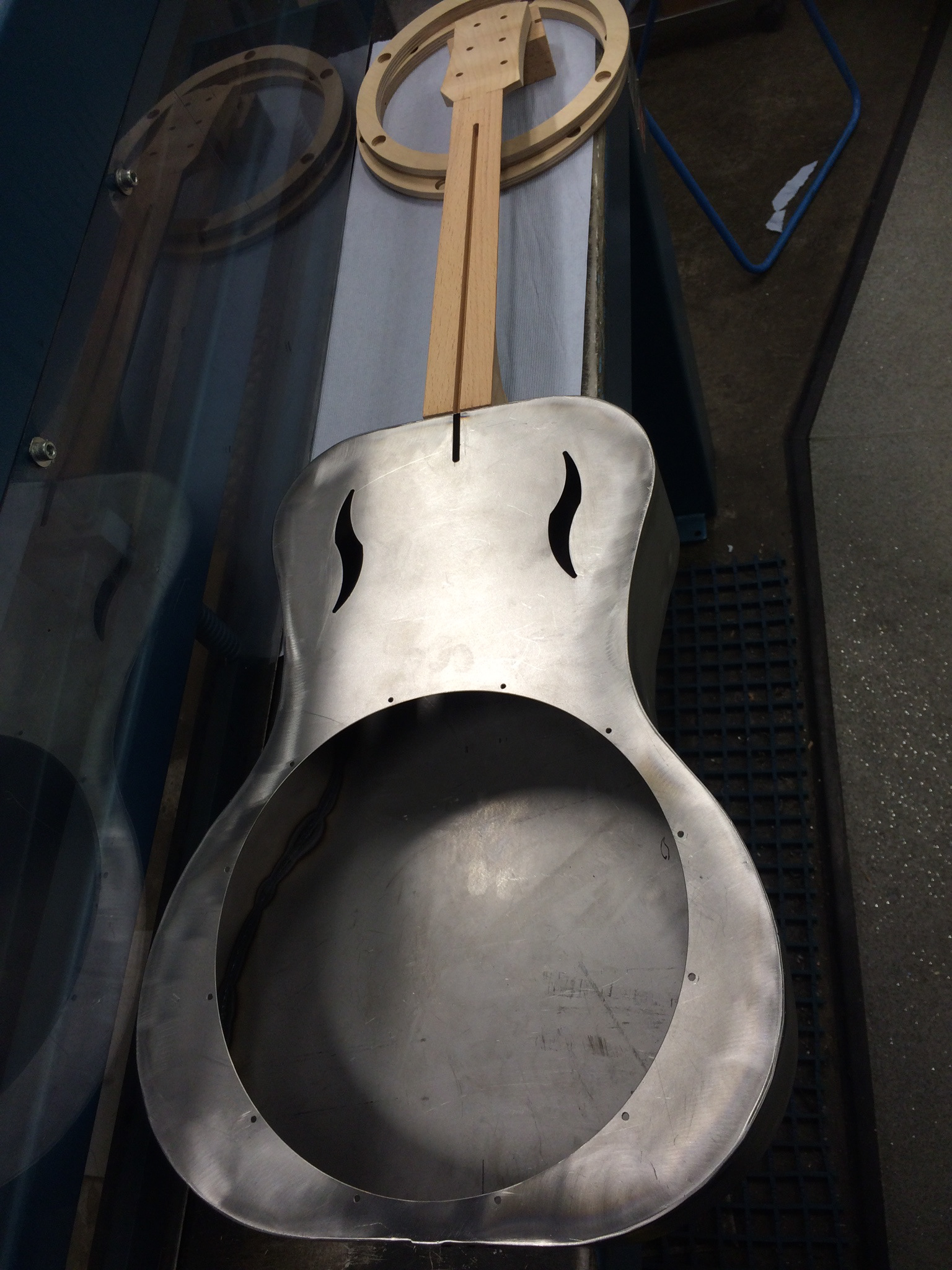
The Assembled Metal Body, Neck and Headstock of the Resonator Guitar
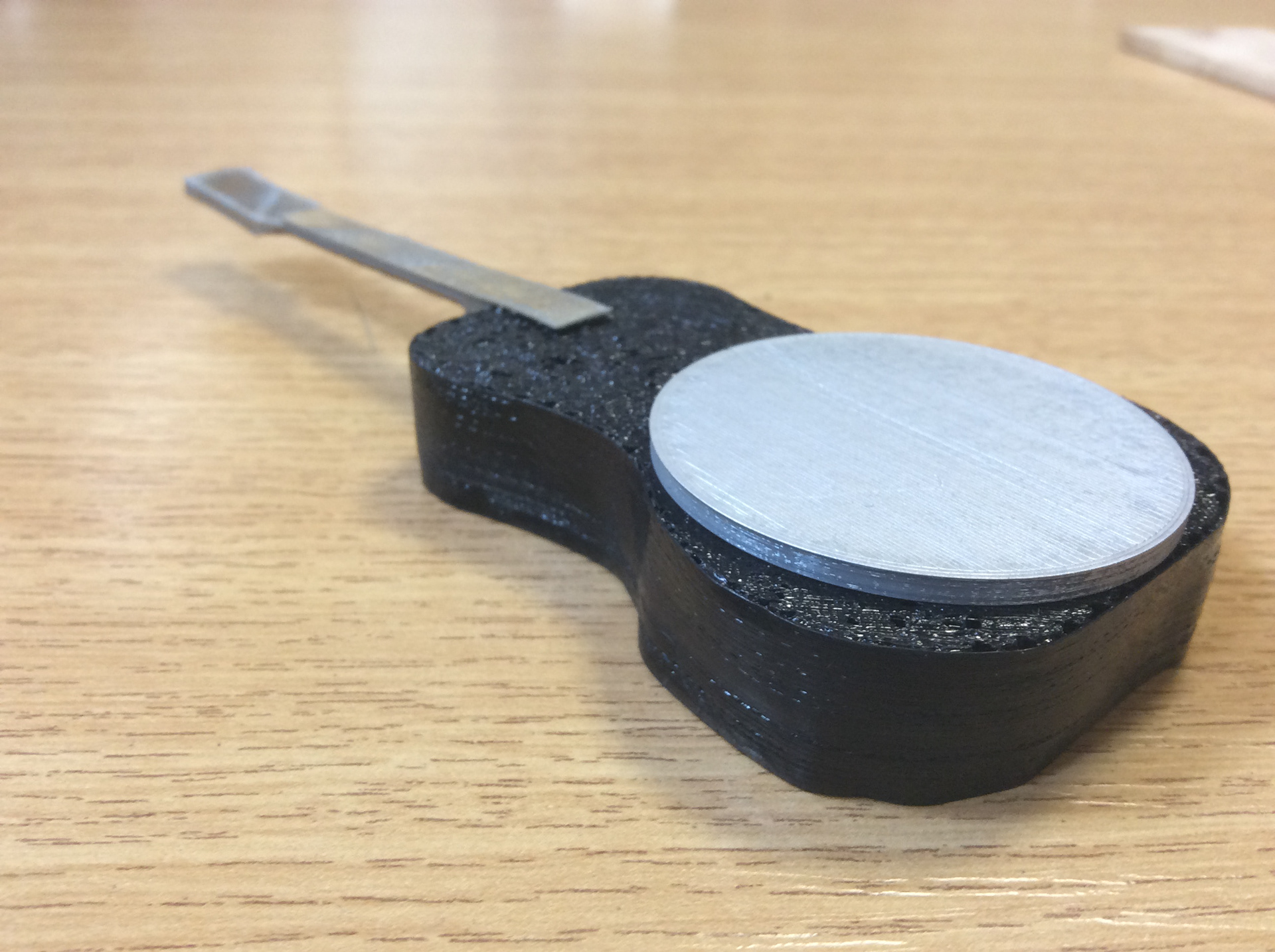